CAD, or Computer-Aided Design, isn’t just about drawing lines on a screen; it’s the backbone of modern design and manufacturing. From sleek sports cars to towering skyscrapers, CAD software empowers engineers, architects, and designers to create, visualize, and refine their ideas with unprecedented precision and efficiency. This exploration delves into the multifaceted world of CAD, covering everything from the basics of different software packages to the advanced techniques used in cutting-edge industries.
We’ll unpack the intricacies of file formats, explore the role of CAD in various sectors, and even peek into the future with virtual reality and simulation applications.
This deep dive will equip you with a solid understanding of CAD’s capabilities and its transformative impact on the design process. We’ll cover the practical aspects of using CAD software, discuss the importance of choosing the right tools for the job, and highlight the innovative ways CAD is shaping the future of design and manufacturing.
CAD Software Comparison
Choosing the right CAD software depends heavily on your specific needs and project goals. AutoCAD, Revit, and Fusion 360 each offer unique strengths and weaknesses, catering to different user profiles and workflows. This comparison will highlight the key differences to help you make an informed decision.
User Interface Comparison
The user interfaces of AutoCAD, Revit, and Fusion 360 are significantly different, reflecting their distinct design philosophies and target audiences. AutoCAD, a veteran in the field, boasts a customizable interface but can feel somewhat dated compared to its newer competitors. Revit, built for Building Information Modeling (BIM), presents a more structured and project-centric workspace. Fusion 360, aiming for a more intuitive experience, offers a streamlined and modern interface that integrates seamlessly with other Autodesk products.
Software | Strengths | Weaknesses | Target User |
---|---|---|---|
AutoCAD | Highly customizable, extensive library of tools, industry-standard compatibility. | Steeper learning curve, can feel cluttered, less intuitive than newer software. | Experienced drafters, engineers, and designers working on 2D and 3D projects. |
Revit | Excellent for BIM workflows, strong collaboration features, robust analysis tools. | Limited flexibility outside of BIM, steeper learning curve, not ideal for simple 3D modeling. | Architects, structural engineers, and MEP engineers focused on building design. |
Fusion 360 | Intuitive interface, cloud-based collaboration, integrated CAM capabilities. | Can be less powerful than dedicated CAD software for specific tasks, some features are still developing. | Product designers, hobbyists, and makers needing a versatile and integrated design solution. |
Rendering Capabilities
Each software’s rendering capabilities vary significantly. AutoCAD’s rendering is functional but lacks the photorealism and advanced features found in other options. Revit offers decent rendering quality, primarily focused on realistic visualizations of buildings and interiors. Fusion 360, however, stands out with its cloud-based rendering capabilities, allowing for high-quality renders without needing powerful local hardware. While Fusion 360’s rendering might not be as advanced as dedicated rendering software like V-Ray, it offers a good balance of quality and accessibility.
Simple 3D Model Workflow Comparison
Creating a simple 3D cube illustrates the workflow differences. In AutoCAD, one would use the 3D modeling commands (like BOX or EXTRUDE) to create the cube, relying heavily on precise coordinate input and command line interactions. Revit’s approach involves using families and parameters, defining the cube’s dimensions within a project context. This method is more structured but less intuitive for simple tasks.
Fusion 360 provides a more intuitive, direct modeling approach. The user could simply use the basic shapes tool, select a cube, and define its dimensions using a visual interface, making the process quicker and more user-friendly. The key differences lie in the level of control, the emphasis on parametric modeling, and the overall user experience.
CAD File Formats
Okay, so we’ve talked about CAD software, and now it’s time to dive into the nitty-gritty of file formats. Choosing the right file format is crucial for smooth collaboration and data exchange, especially in larger projects. Getting this wrong can lead to headaches and lost time, so let’s get clear on the major players.
Understanding the nuances of different CAD file formats is key to efficient project management and preventing compatibility issues. The three most common formats—DWG, DXF, and STEP—each have their strengths and weaknesses, impacting how easily you can share and use your designs.
DWG, DXF, and STEP File Format Differences
Here’s a breakdown of the key differences between these three popular CAD file formats. Understanding these differences will help you make informed decisions about which format to use in different situations.
- DWG (Drawing): This is the native file format for AutoCAD. It’s a proprietary format, meaning it’s owned and controlled by Autodesk. It generally offers the best preservation of design data and features, including layers, blocks, and other complex elements. However, its proprietary nature can limit compatibility with other CAD software.
- DXF (Drawing Exchange Format): DXF is also an Autodesk format, but it’s designed for interoperability. It’s a text-based format that’s meant to be more easily shared between different CAD programs. While it can preserve much of the design data, it sometimes loses some of the more nuanced features of a DWG file. Think of it as a more “universal” language compared to DWG’s “Autodesk-only” dialect.
- STEP (Standard for the Exchange of Product model data): STEP is a completely different animal. It’s an open, international standard specifically designed for exchanging 3D model data between different CAD systems and other software applications. It’s great for sharing complex designs across platforms and is particularly useful in collaborative projects involving multiple companies or departments using different software. However, it can be more complex to work with and might not support all the features of proprietary formats like DWG.
Advantages and Disadvantages of Each Format for Data Exchange
Let’s look at the pros and cons of each format when it comes to sharing your designs with others.
- DWG:
- Advantages: Preserves most design details, excellent for within-Autodesk workflows.
- Disadvantages: Limited compatibility with non-Autodesk software, potential for data loss when opened in other programs.
- DXF:
- Advantages: Better interoperability than DWG, relatively simple format.
- Disadvantages: Can lose some design details during conversion, not ideal for complex designs.
- STEP:
- Advantages: Excellent interoperability across different CAD systems and software, suitable for complex designs.
- Disadvantages: Can be more complex to work with than DWG or DXF, might not support all design features.
Best Practices for Managing Different CAD File Formats in Collaborative Design Projects
Effective file format management is crucial for smooth collaboration. Here’s how to keep things running smoothly.
- Establish a standardized file format: Choose a single format for the project, preferably one compatible with all participants’ software. This prevents conversion issues and ensures everyone works with the same data.
- Version control: Use a version control system (like Git) to track changes and prevent overwriting of files. This is especially important in collaborative projects where multiple people are working on the same design simultaneously.
- Regular backups: Always back up your files regularly to prevent data loss. Cloud storage or local backups are both viable options.
- Clear communication: Ensure everyone on the team understands the chosen file format and any associated limitations. This prevents confusion and delays.
- Use a central repository: A shared network drive or cloud storage service can be used as a central location for all project files, making them easily accessible to all team members.
CAD in Different Industries

CAD, or Computer-Aided Design, has revolutionized numerous industries, impacting design, manufacturing, and overall efficiency. Its applications span a wide range, from the intricate designs of aircraft to the detailed blueprints of buildings. This section explores CAD’s vital role in several key sectors.
CAD in the Automotive Industry
The automotive industry heavily relies on CAD for both design and manufacturing. From initial concept sketches to the final production-ready models, CAD software allows engineers to create highly detailed 3D models of vehicles and their components. This enables them to perform simulations, analyze performance characteristics, and identify potential design flaws before physical prototypes are even built. Furthermore, CAD integrates seamlessly with CAM (Computer-Aided Manufacturing) systems, allowing for the direct translation of digital designs into manufacturing instructions for robotic assembly lines and CNC machining.
This streamlined process significantly reduces lead times and improves overall manufacturing precision. Think of the complex curves of a modern car body – designing that accurately and efficiently without CAD would be practically impossible. Major automakers use software like CATIA, NX, and Creo Parametric extensively for these processes.
CAD in Architectural Design and Building Information Modeling (BIM)
CAD plays a critical role in architectural design, extending far beyond simple 2D drawings. The integration of Building Information Modeling (BIM) has transformed the architectural process, allowing for the creation of intelligent 3D models that contain far more information than traditional CAD models. These models aren’t just visual representations; they include data on materials, structural elements, and even building systems.
This rich dataset allows for better collaboration between architects, engineers, and contractors, leading to more efficient design processes and reduced construction errors.The importance of BIM lies in its ability to provide a single source of truth for all project information. This allows stakeholders to visualize the building in its entirety, analyze its performance, and make informed decisions throughout the project lifecycle.
- Centralized Data Management: BIM provides a central repository for all project data, ensuring everyone works from the same information.
- Improved Collaboration: Different disciplines can work concurrently on the same model, improving coordination and reducing conflicts.
- Enhanced Visualization: 3D models allow for better visualization and understanding of the design, facilitating communication and decision-making.
- Clash Detection: BIM software can detect clashes between different building systems, preventing costly errors during construction.
- 4D and 5D Modeling: BIM extends beyond 3D by incorporating time (4D) and cost (5D) data, enabling better project scheduling and cost control.
Commonly used software in architectural design includes Autodesk Revit, ArchiCAD, and Vectorworks.
CAD in Aerospace Engineering
Aerospace engineering demands extremely high levels of precision and accuracy. CAD software is essential in designing aircraft, spacecraft, and their components. The complexity of these designs requires sophisticated software capable of handling intricate geometries and performing complex simulations. This is particularly crucial for analyzing aerodynamic performance, structural integrity, and thermal management. Software like CATIA, NX, and SolidWorks are widely used, often in conjunction with specialized aerospace simulation tools.
These tools allow engineers to model and analyze airflow, stress distributions, and other critical factors that ensure the safety and performance of aerospace vehicles. For example, designing a wing with optimal lift and minimal drag requires detailed computational fluid dynamics (CFD) simulations, often integrated directly within the CAD environment. The precision required in aerospace engineering makes CAD an indispensable tool.
CAD Modeling Techniques
Okay, so we’ve covered the basics of CAD, different file formats, and how it’s used across various industries. Now let’s dive into the nitty-gritty of actuallymaking* things in CAD software. This section focuses on the core techniques used to build 3D models, from the simple to the incredibly complex. We’ll explore parametric modeling, constraint-based modeling, and different solid modeling approaches, comparing them to surface modeling.
Parametric Modeling with Autodesk Inventor
Parametric modeling is like building with LEGOs, but way more powerful. Instead of just snapping pieces together, you define relationships between parts, so changes to one part automatically update connected parts. Let’s see how this works in Autodesk Inventor. Imagine we’re designing a simple bracket.
- Sketch Creation: We start by sketching the profile of the bracket in a 2D plane. This might involve drawing lines, arcs, and other geometric shapes using Inventor’s sketching tools. We’ll define dimensions (length, width, thickness) to ensure accuracy.
- Extrusion: Next, we use the “extrude” feature. This takes our 2D sketch and pulls it out into three dimensions, giving it depth. The extrusion distance is a parameter we can easily change later.
- Adding Features: We can then add features like holes, fillets (rounded edges), and cutouts. Each feature is also parametric, meaning we can adjust its size and position without having to rebuild the entire part from scratch. For example, we could add a hole with a specified diameter and location.
- Relationships and Constraints: The key here is the relationships between features. For instance, we might constrain the hole to be centered on the bracket’s width. If we change the bracket’s width, the hole automatically moves to stay centered.
- Modifying Parameters: Now comes the magic. Let’s say we need a slightly wider bracket. We simply change the width parameter in our initial sketch, and Inventor automatically updates the entire model, including the hole’s position and the overall dimensions. This ensures design consistency and saves a ton of time.
Constraint-Based Modeling
Constraint-based modeling is all about defining relationships between geometric elements. These constraints ensure that the model behaves as expected, even when parameters change. Think of it as setting rules for your design. For example, you might constrain two lines to be perpendicular or two surfaces to be parallel. This prevents accidental inconsistencies and makes the model more robust.
This technique is vital in assembly design, ensuring parts fit together correctly. A common application is in designing a robotic arm where joint angles are constrained to ensure proper movement. If a joint’s angle exceeds a defined limit, the constraint would prevent it from moving further, avoiding a collision or malfunction.
Solid Modeling vs. Surface Modeling
Solid modeling and surface modeling are two different approaches to creating 3D models. Solid modeling creates a complete 3D solid object with volume and mass. Think of it like carving a sculpture from a block of wood—you start with a solid and remove material to create the desired shape. Surface modeling, on the other hand, focuses on creating surfaces.
It’s like creating a shell; you define the outer surfaces, but there’s no inherent volume or mass. This is useful for things like car bodies or complex organic shapes where precise surface definition is paramount, but internal structure isn’t critical. Solid modeling is generally preferred for engineering applications because it provides a complete representation of the part, allowing for more accurate analysis and manufacturing.
Surface modeling finds its niche in design visualization and applications where the internal structure is not a concern.
CAD and 3D Printing
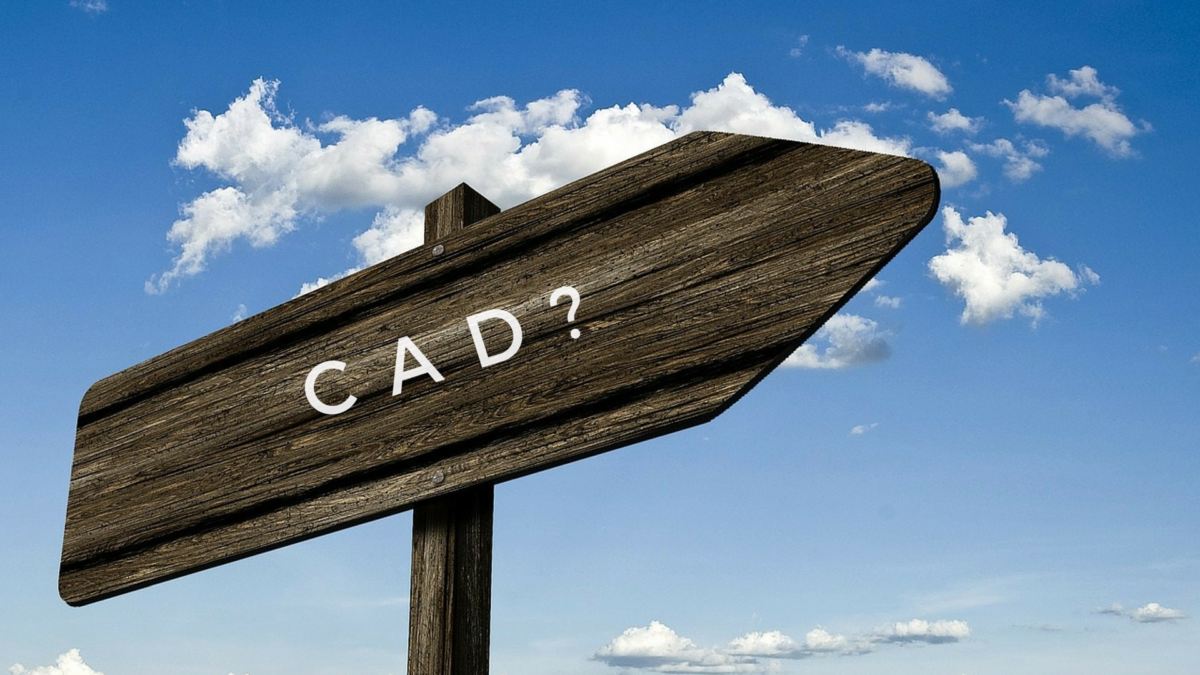
CAD (Computer-Aided Design) and 3D printing are a powerful combination, revolutionizing prototyping, manufacturing, and design processes across numerous industries. The ability to translate a digital design directly into a physical object has dramatically shortened lead times and opened up new possibilities for creativity and innovation. However, understanding the nuances of preparing a CAD model for 3D printing is crucial for a successful outcome.Preparing a CAD model for 3D printing involves several key steps and considerations to ensure the final product meets the designer’s expectations.
Failure to properly prepare the model can lead to printing errors, wasted material, and ultimately, a flawed final product. Key aspects include file format selection, resolution optimization, and the implementation of support structures where necessary.
File Format Considerations for 3D Printing
The most common file format used in 3D printing is STL (Stereolithography). STL files represent a 3D model as a collection of triangular facets, making them relatively simple for 3D printers to interpret. Other formats, such as OBJ, can also be used, but they often require conversion to STL before printing. The choice of file format impacts the fidelity of the final print; higher-resolution STL files, with more triangles, will generally result in a smoother, more accurate representation of the original CAD model, but also increase file size and processing time.
Conversely, lower-resolution files are quicker to process but may exhibit a more faceted or less refined appearance.
Resolution and its Impact on 3D Prints
The resolution of a CAD model directly influences the quality of the 3D-printed object. Resolution refers to the level of detail captured in the model, often expressed in terms of the number of polygons or facets used to represent the surface. Higher resolution means more polygons, leading to smoother curves and finer details in the printed object. However, extremely high-resolution models can significantly increase processing time and file size, potentially overwhelming the 3D printer’s capabilities.
Finding the optimal balance between detail and processing efficiency is a crucial aspect of preparing the model for 3D printing. For example, a highly detailed model of a human skull might require a higher resolution than a simple geometric shape like a cube.
Support Structures in 3D Printing
Many 3D printing techniques require support structures for overhanging or intricate geometries to prevent sagging or deformation during the printing process. Support structures are temporary scaffolding that the printer creates alongside the main model. These structures are later removed manually or through post-processing techniques. The design and placement of support structures are critical; insufficient support can lead to print failures, while excessive support can add to material costs and post-processing time.
CAD software often includes tools to automatically generate support structures, allowing users to specify parameters such as density and placement. The choice of support structure material also influences the ease of removal and potential damage to the printed object.
Limitations of CAD Models in 3D Printing
While CAD models are essential for 3D printing, certain limitations exist. The inherent limitations of the printing technology itself, such as layer height and nozzle size, can affect the final accuracy and surface finish of the printed object. Complex geometries or extremely fine details might be challenging to reproduce accurately. Also, the material properties of the 3D printing filament or resin can influence the strength, durability, and overall appearance of the final print.
For instance, a CAD model designed for a high-strength application might require specific material selection and print settings to achieve the desired properties.
Generating a Printable STL File from a CAD Model
Generating an STL file from a CAD model typically involves exporting the model from the CAD software. Most CAD packages support direct export to STL format. Before exporting, it’s crucial to check the model for any errors or inconsistencies, such as non-manifold geometry or gaps in the surface. These errors can prevent successful 3D printing. After exporting, the STL file can be inspected using dedicated software to ensure its integrity and suitability for 3D printing.
This often includes checking for self-intersections, open surfaces, and other potential issues that could lead to print failures. Many slicer programs offer tools for inspecting and repairing STL files before sending them to the 3D printer.
History of CAD Technology

The evolution of Computer-Aided Design (CAD) technology is a fascinating journey reflecting advancements in computing power and graphical capabilities. From its humble beginnings as a tool for automating drafting tasks, CAD has transformed into a sophisticated suite of software crucial across countless industries, impacting everything from architecture and engineering to manufacturing and animation. Its development is intrinsically linked to the growth of computer graphics and processing power, allowing for increasingly complex and realistic simulations.The impact of computer graphics and processing power on the evolution of CAD software is undeniable.
Early CAD systems were limited by the processing power and memory available, resulting in simple 2D line drawings. As computers became faster and more powerful, CAD software could handle more complex geometries and larger datasets, leading to the development of 3D modeling capabilities. The advancements in graphical user interfaces (GUIs) also played a crucial role, making CAD software more user-friendly and accessible to a wider range of users.
The development of powerful graphics cards, capable of rendering complex 3D models in real-time, further revolutionized the field.
Early Developments and 2D CAD
The earliest forms of CAD emerged in the 1960s, initially focused on automating the drafting process. Systems like SKETCHPAD, developed by Ivan Sutherland at MIT in 1963, were groundbreaking. While primitive by today’s standards, SKETCHPAD demonstrated the potential of using computers for design. These early systems were largely limited to 2D drafting, using vectors to represent lines and curves.
The use of digitizers and plotters allowed for the creation of precise drawings, but the process was still relatively slow and cumbersome compared to modern CAD software. These early systems laid the foundation for the development of more sophisticated 2D CAD software throughout the 1970s and 80s, which saw widespread adoption in industries like architecture and engineering.
The Rise of 3D CAD Modeling
The transition from 2D to 3D CAD modeling marked a significant leap forward in design capabilities. While 2D CAD was sufficient for representing simple shapes, 3D modeling allowed designers to create and manipulate three-dimensional objects, offering a far more realistic representation of the final product. The development of powerful algorithms and increased processing power were key factors in this transition.
Early 3D CAD systems used wireframe modeling, representing objects as a collection of lines and curves. Subsequently, surface modeling techniques were developed, allowing for the creation of more realistic representations of curved surfaces. Solid modeling, which represents objects as solid volumes, became the dominant approach, enabling more accurate analysis and simulation. Software like AutoCAD, Pro/ENGINEER (now PTC Creo), and SolidWorks emerged as industry leaders, each offering unique features and capabilities.
The ability to create and manipulate 3D models significantly improved the design process, allowing for better visualization, analysis, and collaboration.
A Timeline of Key Advancements
- 1963: Ivan Sutherland develops SKETCHPAD, a pioneering interactive computer graphics system laying the groundwork for CAD.
- 1960s-1970s: Early CAD systems emerge, primarily focused on 2D drafting and automating design tasks. These systems were often proprietary and expensive.
- 1980s: The development of powerful microprocessors and improved graphics capabilities lead to the widespread adoption of 2D CAD software.
- Late 1980s – 1990s: 3D CAD modeling becomes increasingly prevalent, with the introduction of solid modeling techniques and user-friendly interfaces.
- 1990s – Present: Advancements in processing power, graphics capabilities, and algorithms lead to increasingly sophisticated CAD software with features like parametric modeling, simulation, and collaboration tools. The integration of CAD with other software such as CAM (Computer-Aided Manufacturing) and CAE (Computer-Aided Engineering) becomes more common.
CAD and Virtual Reality (VR)
The integration of CAD models with virtual reality (VR) is revolutionizing the design process, offering engineers and designers unprecedented opportunities for immersive design review and visualization. This allows for a more intuitive understanding of complex designs and facilitates better collaboration among team members. While still a developing field, the potential for increased efficiency and improved design quality is significant.VR’s impact on CAD design stems from its ability to create a three-dimensional, interactive environment where users can experience the design as if it were physically present.
This immersive experience goes beyond traditional 2D screen displays, offering a deeper understanding of spatial relationships, proportions, and overall design aesthetics.
VR Advantages in CAD Design and Collaboration
Using VR for CAD significantly improves design review and collaboration. Imagine a team scattered across the globe, all simultaneously experiencing and interacting with the same 3D model, offering feedback in real-time. This reduces ambiguity and allows for faster iteration cycles. Furthermore, the immersive nature of VR can highlight potential design flaws or inconsistencies that might be missed in a traditional 2D setting, leading to better problem-solving and ultimately, a higher quality final product.
The ability to “walk through” a virtual building, for example, provides a much clearer understanding of space and flow than any 2D blueprint ever could. This translates to tangible cost savings by catching errors early in the design process, preventing costly rework later.
VR Disadvantages in CAD Design and Collaboration
Despite the advantages, there are limitations to consider. The initial investment in VR hardware and software can be substantial, representing a significant barrier to entry for some companies. Furthermore, the learning curve for effectively using VR software can be steep, requiring dedicated training and potentially impacting productivity initially. Motion sickness is also a potential concern for some users, limiting the length of VR sessions and potentially affecting the effectiveness of design reviews.
Finally, the level of detail achievable in VR is still evolving, and some very complex CAD models might require significant processing power to render smoothly in a VR environment, potentially leading to performance bottlenecks.
Workflow for Incorporating VR into a CAD Design Process
A typical workflow might involve exporting the CAD model in a suitable format (such as FBX or glTF) compatible with VR software. The model is then imported into a VR application, where it can be viewed and manipulated using VR controllers. Design reviews can be conducted remotely or in person, with participants using VR headsets to collaboratively explore the model.
Feedback is gathered in real-time, and changes are made to the original CAD model, iterating through this process until the design is finalized. This workflow requires careful planning and coordination to ensure seamless integration between the CAD software and the VR environment. It’s crucial to establish clear communication protocols and define roles for participants to maximize efficiency and ensure a productive design review process.
For instance, a team leader might guide the review, highlighting specific areas for discussion, while other team members provide feedback and suggest improvements. This collaborative aspect is a key strength of VR in the CAD workflow.
CAD and Simulation
CAD software isn’t just for creating pretty pictures; it’s a powerful tool for simulating real-world scenarios. By leveraging the geometric data within a CAD model, engineers and designers can predict how a product will perform under various conditions before it’s even built, saving time, money, and resources. This is achieved primarily through techniques like Finite Element Analysis (FEA) and Computational Fluid Dynamics (CFD).CAD models provide the crucial geometric foundation for both FEA and CFD simulations.
FEA breaks down a complex CAD model into smaller, simpler elements (think tiny cubes or tetrahedrons) and uses mathematical equations to analyze stress, strain, and deformation under applied loads. CFD, on the other hand, focuses on fluid flow and heat transfer. The CAD model defines the boundaries for the fluid flow, allowing the software to calculate pressure, velocity, and temperature distributions.
The accuracy of the simulation directly depends on the accuracy and completeness of the underlying CAD model. A flawed model will lead to flawed simulation results, potentially resulting in costly design failures.
Finite Element Analysis (FEA) Using CAD Models
FEA uses the CAD model’s geometry to create a mesh, a network of interconnected elements that approximate the shape of the part. Different element types (e.g., tetrahedral, hexahedral) are chosen based on the complexity of the geometry and the desired accuracy. Once the mesh is generated, material properties (like Young’s modulus and Poisson’s ratio) are assigned to each element.
Loads and boundary conditions (constraints on the model’s movement) are then defined. The FEA software solves a system of equations to determine the stress, strain, and displacement at each element. The results are then visualized, often as color-coded stress contours or deformation plots, allowing engineers to identify potential weak points or areas of high stress concentration. For example, a CAD model of a car chassis could be subjected to FEA to simulate the stresses during a crash test, helping engineers design a safer and more robust structure.
Computational Fluid Dynamics (CFD) Using CAD Models
Similar to FEA, CFD uses the CAD model to define the geometry of the flow domain. A mesh is created, but this time it’s used to discretize the fluid flow field. The software solves the Navier-Stokes equations, which govern fluid motion, using numerical methods. Boundary conditions are defined, such as inlet and outlet velocities, pressures, and temperatures.
The simulation predicts velocity, pressure, and temperature distributions throughout the flow field. For instance, a CAD model of an airplane wing could be used in CFD simulation to analyze airflow patterns and optimize the wing’s aerodynamic performance. This could involve simulating various angles of attack to determine the most efficient design.
Setting Up a Simple Simulation Using a CAD Model
The process generally involves these steps: First, a CAD model is created. Next, the model is imported into simulation software (like ANSYS, Abaqus, or COMSOL). Then, the model is meshed; this step involves dividing the model into smaller elements. Next, material properties and boundary conditions are defined. The simulation is then run, and the results are post-processed and analyzed.
Consider a simple example: simulating the stress on a simple cantilever beam. The beam’s geometry is created in CAD, imported into the simulation software, meshed, and then a load is applied at the free end. The simulation will calculate the stress and deflection along the beam.
Importance of Accurate CAD Models in Simulation
The accuracy of simulation results is directly tied to the accuracy of the CAD model. Geometric inaccuracies, missing features, or poorly defined surfaces can lead to significant errors in the simulation. A simplified or idealized CAD model might produce results that are far from reality, leading to incorrect design decisions. For example, neglecting small holes or fillets in a part’s geometry can significantly affect stress concentrations, leading to an underestimation of failure risk.
Therefore, creating a detailed and accurate CAD model is crucial for obtaining reliable and meaningful simulation results. This ensures the design is robust and performs as expected in the real world.
Okay, so CAD, right? Like, designing stuff on the computer. But managing all those designers and their payroll? That’s where HR comes in, and you need a solid hris systems to handle everything. Back to CAD – once you’ve got the HR stuff sorted, you can focus on actually making awesome designs.
Advanced CAD Features
Okay, so we’ve covered the basics of CAD. Now let’s dive into some seriously cool, advanced features that take CAD design to the next level. These aren’t just bells and whistles; they’re game-changers that allow for far more complex and efficient designs across various industries. We’ll be looking at surface modeling, freeform design, and generative design, exploring their applications and comparing their strengths.Surface modeling, freeform design, and generative design represent significant advancements in CAD capabilities, enabling the creation of intricate and complex geometries that were previously difficult or impossible to achieve using traditional solid modeling techniques.
These methods offer designers increased flexibility and efficiency, particularly in fields requiring organic shapes or highly optimized designs.
Surface Modeling
Surface modeling focuses on creating 3D shapes defined by mathematical surfaces rather than solid volumes. Think of it like sculpting with digital clay. Instead of defining a solid object, you’re defining the outer skin. This is crucial for creating aesthetically pleasing and aerodynamic designs, especially in automotive, aerospace, and product design. For example, designing a sleek, curved car body is much easier with surface modeling than with traditional solid modeling, where you’d have to create and combine numerous solid primitives.
The result is a more organic and refined shape, often with improved functionality. Different surface types, like NURBS (Non-Uniform Rational B-Splines), allow for precise control over curvature and smoothness. The process often involves manipulating control points to adjust the surface shape.
Freeform Design
Freeform design takes surface modeling a step further, allowing for even more organic and complex shapes. It’s less about precise mathematical definitions and more about intuitive shaping and manipulation. Think of it like digital sculpting, but with even more control and precision. This is perfect for creating designs that defy traditional geometric constraints, such as architectural models with flowing curves, or organic-looking product designs that mimic natural forms.
Software tools often incorporate intuitive interfaces with features like sketching, sculpting, and direct manipulation tools to aid in the freeform design process. A good example is designing a unique piece of furniture with sweeping curves and irregular shapes—something impossible to create with basic solid modeling techniques.
Generative Design
Generative design is a revolutionary approach that uses algorithms and artificial intelligence to explore a vast design space and automatically generate multiple design options based on specified parameters and constraints. You input your design goals (e.g., strength, weight, material, manufacturing process), and the software generates a range of possible solutions. This significantly speeds up the design process and often leads to innovative solutions that a human designer might not have considered.
Consider designing a lightweight but strong bicycle frame. Generative design software can explore countless variations of tube shapes, thicknesses, and connections, ultimately producing a design that is both lighter and stronger than anything a human designer could create through traditional methods. This approach is becoming increasingly popular in aerospace, automotive, and architectural design.
Comparison of Advanced CAD Features Efficiency
The efficiency of surface modeling, freeform design, and generative design depends heavily on the specific design context and the software used. Surface modeling is generally efficient for creating smooth, curved surfaces, but it can become complex for highly intricate designs. Freeform design offers greater flexibility but might require more time and expertise. Generative design excels at exploring many design options quickly, but setting up the parameters and constraints can be time-consuming.
Often, a combination of these techniques is used to achieve the best results. For instance, a designer might use generative design to explore initial design concepts, then refine the selected design using surface modeling and freeform techniques to achieve the desired aesthetic and functionality.
CAD Security and Data Management
Protecting your CAD designs isn’t just about keeping your work safe from prying eyes; it’s about safeguarding your intellectual property, maintaining project integrity, and ensuring smooth collaboration. Data breaches can lead to significant financial losses, reputational damage, and legal issues. Robust security measures are essential for any organization using CAD software.CAD data security involves implementing strategies to prevent unauthorized access, modification, or destruction of design files.
This is particularly crucial in collaborative projects where multiple individuals may be accessing and modifying the same files simultaneously. Furthermore, the increasing reliance on cloud-based storage and collaboration tools necessitates a proactive approach to data security to mitigate risks associated with internet-based threats.
Methods for Protecting CAD Data
Effective CAD data protection involves a multi-layered approach. This includes employing strong passwords and access controls, regularly updating software to patch security vulnerabilities, and implementing robust backup and recovery systems. Version control systems are also crucial for tracking changes and reverting to previous versions if necessary. Consider using encryption both in transit and at rest for sensitive data, and restrict access based on user roles and responsibilities.
Regular security audits should be conducted to identify and address potential weaknesses.
CAD File Management and Archiving
A well-defined plan for managing and archiving CAD files is critical for maintaining data integrity and accessibility. This involves establishing a clear naming convention for files, using a centralized storage system, and implementing a version control system to track revisions. Regular backups should be performed to a separate location, ideally offsite, to protect against data loss due to hardware failure or disaster.
For long-term archiving, consider using a robust digital asset management system that allows for efficient retrieval and preservation of files. A robust metadata system should be in place to facilitate efficient searching and retrieval of files based on various criteria, such as project name, date, and author. Regular purging of outdated or irrelevant files should also be implemented to manage storage space efficiently.
Consider implementing a data retention policy that Artikels how long CAD files should be kept and under what circumstances they can be deleted. For example, a company might retain project files for a specified number of years after project completion or until the product is no longer in use.
Final Summary
So, there you have it – a whirlwind tour through the exciting world of CAD! From the historical evolution of this powerful technology to its cutting-edge applications in VR and simulation, we’ve covered a lot of ground. Remember, mastering CAD isn’t just about learning the software; it’s about understanding the design process, embracing creativity, and leveraging the power of technology to bring your ideas to life.
Whether you’re a seasoned pro or just starting out, the world of CAD is vast and ever-evolving, so keep exploring and innovating!
General Inquiries
What’s the difference between 2D and 3D CAD?
2D CAD focuses on flat, two-dimensional drawings, like blueprints. 3D CAD creates three-dimensional models, allowing for more realistic visualizations and simulations.
Is CAD software expensive?
Costs vary widely depending on the software and licensing options. Some offer free versions with limited features, while others require subscriptions or one-time purchases, often ranging from hundreds to thousands of dollars.
How long does it take to learn CAD?
Learning CAD takes time and practice. The learning curve depends on your prior experience and the complexity of the software, but expect to invest several weeks or months to gain proficiency.
What are some common career paths using CAD skills?
CAD skills are highly sought after in many fields, including engineering, architecture, manufacturing, game design, and more. Jobs might include CAD technician, drafter, designer, or engineer.
Can I use CAD for animation or game design?
Yes! CAD models can be imported into animation and game engines. While not specifically designed for animation, CAD provides a solid foundation for creating 3D assets.